

501 South Main St. Galena Park, TX 77547
713.922.9968
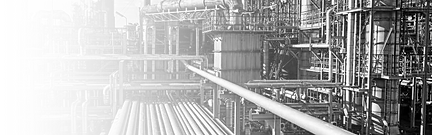
Featured Projects
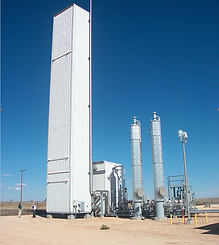

Documents:
Nitrogen Rejection Plant
The NRU #1 is a BCCK designed Nitrogen rejection plant designed for an inlet volume of 6 MMCF/D of natural gas containing 20-30% Nitrogen at 600 psig. The plant is designed to perform at 98% thermal efficiency. Below is a brief description of the operation of the plant and equipment inventory.
PLANT DESIGN SUMMARY
A. GAS COMPRESSION
Gas gathering lines bring the gas to the plant inlet separators which remove gas condensate and water that may condense from the gas stream. Inlet gas compressors are configured with 2 stages of gas compression to boost the inlet gas to the inlet plant operating pressure of 600 psig.
B. GAS DEHYDRATION
The BCCK nitrogen rejection process is a low temperature process which requires removal of saturated water in the gas stream to very low levels to avoid hydration formation in the plant process. High pressure gas from the gas compressors units enters the dehydration skid. A filter separator removes fine levels of liquids that could damage the dehydration beds. There are 2 gas dehydration beds, each filled with molecular sieve desiccant for absorption of the water vapor from the gas stream. The beds are cycled with one in adsorption removing water from the inlet gas stream. Lower pressure gas is heated and passed through the bed to regenerate the bed. Regeneration heat is provided by a small regeneration gas heater.
C. NITROGEN/HYDROCARBON SEPARATION
The plant process utilizes Joule Thompson expansion of the inlet gas stream combined with a complex heat exchange network to achieve temperatures necessary to condense nitrogen from the vapor phase to liquid. The heat exchangers utilized by BCCK for this process are multi-stream plate fin exchangers. The exchangers are of aluminum construction to meet the low temperatures required for the process.
The heart of the separation process is the nitrogen rejection column. The basis for the separation of nitrogen from hydrocarbons is the difference in boiling points. Nitrogen exits the top of the column in the vapor form while methane exits the column bottom as a liquid. The design of the heat exchange network combined with Joule Thompson expansion of the gas stream condenses the nitrogen in the gas stream. A considerable amount of hydrocarbons (primarily methane are also condensed). The nitrogen rejection column is a 62’ tall vertical vessel. Packing sections are installed in the vessel to provide contact surface for boiling vapors and condensing liquids required for the fine separation required.
The column minimizes methane losses in the reject nitrogen stream by the use of a BCCK proprietary overhead condenser. After heat exchange in one pass of the cold plate fin exchanger, a portion of the bottom methane product from the column is expanded in a secondary JT valve. This expansion achieves low temperatures which circulate through the condenser section providing cooling to condense methane vapors to minimize methane losses with the reject N2 stream. Heated vapors from a pass in the cold plate fin exchanger and a trim reboiler provide heat (in the form of heated stripping vapors) to the bottom of the column. These stripping vapors prevent excess nitrogen from leaving with the liquid hydrocarbon stream from the bottom of the column.
The nitrogen reject stream from the top of the tower is warmed in the heat exchange network prior to being vented to atmosphere at an elevated point above the cold box.
D. SALES GAS COMPRESSION AND DELIVERY
There are 2 hydrocarbon streams from the NRU process. After being vaporized and warmed to near plant inlet temperatures, the high pressure (HP) stream exits the NRU at approximately 250 psig and does not require compression. The low pressure (LP) stream from the plant consists of the sidestream of the nitrogen rejection column bottom hydrocarbon product that was expanded across the secondary JT valve to provide column condensing duty. After being fully vaporized and warmed in the heat exchange network, the LP gas flows to the sales gas compressors.
MAJOR PLANT EQUIPMENT
(NRU PROCESS PLANT EQUIPMENT ONLY)
EQUIPMENT TAG
DESCRIPTION
DETAILS
21-801
Waste Heat Recovery Unit
Shell: 5 psig @ 1125 F
Tube: 660 psig @ 1125 F
Duty: 1.4 MMBTU/HR
21-701
Regen Gas Cooler
DP: 660 psig @ 600F
Duty: 641 MBTU/HR
26.501
Inlet Gas Coalescing Filter
8” x 8’-2”
660 psig @ -20/200F
32-102A/B
Dehydrators
30” x 25’ S/S
660 psig @ -20/600F
32-201
Cold Separator
18” x 96”
660 psig @ -150/150 F
21-201
Warm Plate Fin EX
DP: 1100/400/260 psig
DT: -320/150F
21-202
Cold Plate Fin EX
DP: 900/400/260 psig
DT: -320/150F
21-203
Trim Reboiler
Shell: 660 psig
-320/150F
Tube: 400 psig
-320/150F
Duty: 1.5 MMBTU/HR
31-301
N2 Rejection Column
18” x 62’ S/S
400 psig @ -320/150F
29-301
Vane Mist Extractor
14” x 6” x 23”
21-301
Knockback Condenser
33” x 10’
Shell: 260 psig
-320/150F
Tube: 400 psig
-320/150F
Duty: 250 MBTU/HR
No TAG
Regeneration Gas Heater